|
Найбільш характерним механічним впливом є надмірний внутрішній тиск, що може виникати на виробництві при порушенні технологічного режиму, при недостатньому контролі за технологічним процесом, за несправності контрольно-вимірювальних приладів та захисної автоматики.
Зміна тиску у технологічному обладнанні може виникати в результаті:
- порушення матеріального балансу;
- порушення теплового балансу;
- порушення температурного режиму апаратів;
- порушення процесу конденсації парів;
- потрапляння рідин з низькою температурою кипіння у високонагріті апарати.
Порушення матеріального балансу. В основі роботи технологічного пристрою лежить матеріальний та енергетичний (тепловий) баланси.
Згідно матеріального балансу, маса вихідних речовин ∑Gпр процесу повинна дорівнювати масі основних кінцевих продуктів ∑Gкін.пр, незалежно від того, яких змін вони набули в даному апараті, тобто ∑Gпр = ∑Gкін.пр. В цьому випадку в апараті зберігається нормальний (робочий), встановлений для цього апарата тиск.
Якщо ж за деяких причин дана рівність порушується, тоді в апараті утворюється підвищений або знижений тиск. Тиск підвищується, якщо зростає надходження речовин до апарата за незмінної витрати або якщо витрата речовин зменшується при постійному надходженні, тобто коли:
∑Gпр > ∑Gкін.пр (5.1)
Порушення матеріального балансу апаратів виникає при:
- невідповідності продуктивності насосів та компресорів прийнятій інтенсивності заповнення апаратів або дійсній витраті продуктів;
- неправильному з’єднанні апаратів, що працюють з різними тисками;
- збільшенні опорів у витратних, дихальних лініях тощо.
Невідповідність між подачею речовин до апарата та їх витратою. Рідини та гази подають до апаратів та ємностей частіше всього насосами та компресорами. Їх підбирають з таким розрахунком, щоб забезпечити подачу визначеного об’єму речовин. Будь-яка зміна у витраті речовин повинна супроводжуватися зміною продуктивності насоса (компресора). Якщо насос (компресор) буде працювати з тією ж продуктивністю за зниженої витрати або продуктивність насоса (компресора) підвищиться в результаті збільшення числа обертів вала або числа ходів поршня, тоді обов’язково виникне підвищений тиск в апараті.
Небезпека пошкодження апаратів періодичної дії може виникнути в періоди їх заповнення. Відсутність регулюючих пристроїв, а також вимірювачів рівня рідин або тиску газів, недостатній контроль за процесом переповнення можуть бути причиною переповнення апаратів, утворення в них підвищеного тиску та пошкодження корпуса.
Для запобігання переповнення технологічного обладнання рідинами і газами передбачаються наступні заходи:
- застосування лічильників-дозаторів для визначення кількості рідин і газів, що надходять до обладнання;
- застосування пожежонебезпечних рівнемірів та манометрів для контролю рівня або об’єму речовин в апараті (забороняється застосовувати скляні покажчики рівня на апаратах із скрапленими газами під тиском);
- застосування автоматичних систем, що припиняють подачу продуктів відключенням насосів, компресорів і ліній;
- застосування систем автоматичної сигналізації аварійного стану апаратів (наприклад, положення ковпака газгольдера);
- застосування переливних труб на апаратах з рідинами та свічок скидання на апаратах з газами (рис.5.1).

Рисунок 5.1- Захист апарата переливною лінією
1 - рідина із складу; 2 - витратний бак; 3 - наповнювальна лінія; 4 - напірний бак; 5 - переливна труба;
6 - витратна лінія
Переливні труби урізуються в стінки апаратів на висоті максимально припустимого рівня рідини. Вони повинні мати діаметр, більший за діаметр наповнювальної лінії і, з'єднуватися з ємністю, з якої закачується рідина, або з дренажною (аварійною) ємністю.
Найбільш ефективним засобом попередження пошкодження апаратів та ємностей від переповнення є автоматичні системи для зупинки роботи насосів і компресорів або для відключення живильних ліній взагалі при досягненні встановлених рівня рідини та тиску газу в апараті тощо (рис. 5.2).
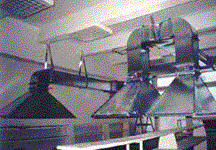
Рисунок 5.2 - Захист газгольдера від переповнення
1-газгольдер; 2 – рухома судина; 3- нерухома судина;4- дифманометр; 5- індукційна катушка; 6- потенціометр;7- засувка на лінії наповнення; 8- витратна лінія
На рис. 5.3 показана принципова схема автоматичного відключення компресора, який подає газ до апарата при досягненні в ньому необхідного тиску. В апараті розміщується датчик тиску, який поєднується з первинним показовим приладом та регулятором. При досягненні граничного тиску газу в апараті регулятор розмикає ланцюг магнітного пускача, завдяки чому зупиняється електродвигун компресора.
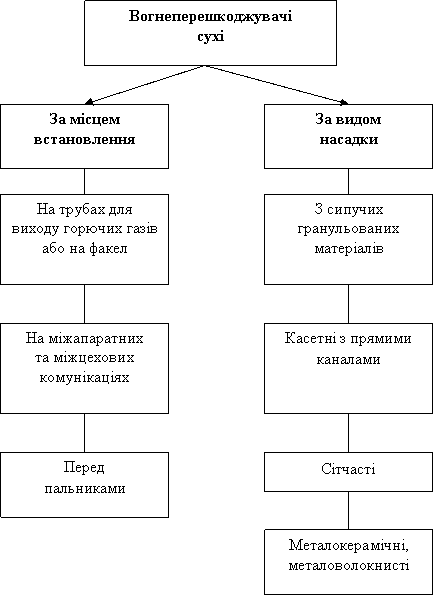
Рисунок 5.3 - Схема автоматичної зупинки та пуску компресора за зміни тиску газу в апараті
1- апарат; 2- компресор; 3 – датчик тиску; 4 – первинний показовий прилад з пневматичним виходом; 5- вторинний сигналізуючий прилад-регулятор з електричним виходом; 6 – кнопка дистанційного включення магнітного пускача; 7- витратна лінія газу
При відновленні витрати газу споживачем тиск в апараті буде зменшуватися, регулятор забезпечить замкнення пускового ланцюга магнітного пускача і компресор знову подасть газ до апарата.
З’єднання апаратів з різними тисками. Якщо апарат працює під тиском, меншим, ніж тиск у джерела, що його живить, тоді за відсутності на з’єднувальних лініях приладів автоматичного регулювання тиску або їх несправності, а також при застосуванні для зниження тиску звичайної запірної арматури в них може виникнути небезпечний тиск. Інколи різниця між величинами тиску пов’язаних між собою апаратів буває дуже великою. Так, наприклад, трубчасті печі установок термічного крекінгу, які працюють при тиску 5-7 МПа, поєднані з випарниками, в яких тиск досягає 6-8 МПа, реактори для одержання поліетилену, що мають робочий тиск 150 МПа, сполучені з сепараторами з робочим тиском 30-40 МПа тощо.
Небезпечними є також підключення систем високого тиску до систем, що працюють при більш низькому тиску.
Так, наприклад, в одному з міст виникла необхідність поєднати два кільця підземних газових мереж низького тиску. Поблизу від газової лінії низького тиску проходила газова лінія середнього тиску. Помилково лінію середнього тиску підключили до газового кільця низького тиску. Надходження газу більш високого тиску до лінії та до приладів, не розрахованих на цей тиск, призвело до утворення масових витоків газу через нещільності у з’єднаннях та до пошкодження газових лічильників. Виникло „здування” полум’я газу, що горів, в газових приладах і в результаті - вибухи та пожежі у житлових будинках.
Профілактика пошкодження з’єднаних апаратів з різним робочим тиском досягається застосуванням (крім запірної засувки) автоматичного редукційного пристрою з манометром і захисним клапаном на стороні меншого тиску (рис.5.4). Запірна засувка повинна знаходитися між апаратом та редукційним пристроєм, поблизу апарата. За невеликих перепадів тиску обидва підключених один до одного апарати необхідно розраховувати на найбільший тиск. Для групи апаратів, які працюють при однаковому тиску та підключені до апарата з високим тиском, достатньо одного редукційного та одного запобіжного клапанів (з манометром), що встановлені на загальній магістралі до першого розгалуження.
Збільшення опорів ліній за наявності в них відкладень та пробок.
Підвищений тиск дуже часто утворюється при збільшенні опору в лініях за насосами, компресорами або апаратами. Це виникає при неповному відкриванні засувок, а також при зменшенні перерізу ліній в результаті відкладень на стінках солей, бруду, коксу, полімерів, кристалогідратів тощо.
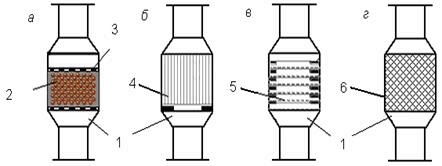
Рисунок 5.4- Редукційні пристрої на апаратах
з надлишковим тиском:
1,2 - апарати відповідно з тиском та ; 3 - редукційний пристрій
З курсу “Технічної механіки рідин і газів” відомо, що втрати напору в системі Нв при транспортуванні речовин (рідин, газів) дорівнюють:
(5.2)
де Нв- втрати напору в системі, мм.в.ст;
Нл - втрати напору по довжині лінії, мм.в.ст.;
Нм - місцеві втрати напору, мм.в.ст.
Величину втрати напору в лініях (для подолання опору і створення необхідної швидкості руху продукту) визначають за формулою:
(5.3)
де - коефіцієнт опору тертя, визначається в залежності від режиму руху продукту;
l- довжина трубопроводу, м;
d- внутрішній діаметр трубопроводу, м;
- швидкість руху продукту в трубопроводі, м/с;
g- прискорення сили ваги, м/с2.
Величину місцевих втрат напору визначають за формулою:
(5.4)
де - коефіцієнт місцевого опору (довідкові дані). Тоді величину втрати тиску в системі можна визначити так:
(5.5)
де ΔP - втрати тиску при збільшенні опору системи, Па;
- густина продукту за робочої температури, кг/м3.
Підставляючи значення формул (5.3) і (5.4) у формулу (5.5), одержимо величину перепаду тиску для подолання опору в системі:
(5.6)
а кінцевий тиск в апараті за наявності відкладень у відвідних трубопроводах можна визначити за формулою:
(5.7)
де Pк - кінцевий тиск у системі при збільшенні опору ліній, Па;
Pп - початковий тиск у системі, Па.
Таким чином, із формули (5.6) видно, що при зменшенні площі перерізу трубопроводу (за умов утворення в ньому відкладень) тиск в системі зростає прямо пропорційно квадрату швидкості руху потоку або відношенню площ нормального та звуженого перерізу або буде відповідно зменшуватися продуктивність системи. Але, як відомо, не всі насоси та компресори мають здатність змінювати свою продуктивність у відповідності до зміни опору лінії. Такої здатності не мають насоси та компресори об’ємної дії – поршневі, шестерінчасті та ротаційні. Для них найбільш небезпечним є повне припинення витрати (закрита засувка, весь переріз труби забитий відкладеннями тощо) за безупинної роботи. В цьому випадку збільшення тиску в лінії безперечно призведе до аварії.
Наприклад, на крекінг-установці нафтопереробного підприємства тимчасово зупинилась робота поршневого „гарячого” насоса. В результаті виникло майже повне закоксування радіантних труб печі глибокого крекінгу. Відновлення роботи насоса призвело до значного підвищення тиску, розриву труб в печі та виникнення пожежі.
Зменшення внутрішнього перерізу трубопроводу може виникнути в результаті утворення різного роду відкладень. Так, наприклад, за низьких температур або за низької температури навколишнього середовища в газових та рідинних лініях (з наявністю вологих вуглеводнів) можливе утворення льодяних та кристалогідратних пробок. Інтенсивність утворення кристалогідратів залежить не тільки від температури та вмісту вологи в газі, але й від тиску газу. Як видно з графіка (рис.5.5), в умовах підвищеного тиску кристалогідрати можуть утворюватися навіть за температури, яка значно вище за 00С. Інтенсивне утворення кристалогідратів може призвести до повного забивання перерізу труби. Відомі відкладення в трубах парафіну, нафталіну, кристалів сірки, капролактаму та інших речовин. Дуже часто виникає накопичення та замерзання води в дренажних лініях.
Для запобігання утворенню відкладень усередині технологічного обладнання і трубопроводів необхідно:
- проводити очистку речовин від твердих часток шляхом відстоювання і фільтрації, від солей - хімічними способами (лугами або кислотами), а також струмами високої напруги на електрознесолюючих установках;
- постійно контролювати і регулювати температурний режим при нагріванні органічних рідин;
- застосовувати спеціальні добавки (інгібітори), які попереджують утворення полімерних відкладень;
- застосовувати для виготовлення апаратів матеріали, які гальмують процес полімеризації;
- проводити попереднє осушення вихідних речовин від вологи (хлористим алюмінієм та кальцієм, силікагелем, виморожуванням тощо);
- застосовувати нагрів тих місць апаратів та трубопроводів, де можливе утворення кристалогідратів;
- застосовувати спеціальні добавки, що розчиняють кристалогідрати (метиловий та етиловий спирти);
- апарати і трубопроводи захищати теплоізоляцією.

Рисунок. 5.5 - Умови утворення кристалогідратів
вуглеводневих газів
1 - пропан; 2- етан; 3 – метан
Підвищення тиску в газових лініях часто виникає через попадання в них рідини (газовий дистилят, водяний конденсат), яка утворює пробки в колінах, вигинах та найбільш низьких місцях. Рідкі пробки в лінії викликають гідравлічні удари та тимчасове припинення подачі газу до місця споживання. Для запобігання конденсації парів газові лінії захищають теплоізоляцією, а в найбільш низьких ділянках газопроводів (та в інших місцях накопичення рідини) встановлюють збірники конденсату. Для уловлювання конденсату, що може знаходитися в газі, перед компресорами влаштовують буферні ємності, а перед апаратами – продувні пристрої для випуску конденсату.
В мірниках, резервуарах та інших апаратах, які пов’язані з атмосферою за допомогою дихальної арматури, підвищений тиск може утворитися через відсутність умов своєчасного видалення пароповітряної суміші (за умов наповнення апарата рідиною). Це частіше всього виникає при забрудненні або заледенінні вогнеперешкоджувача, коли пропускна спроможність дихальної системи не відповідає швидкості наливу рідини. Такі ж причини можуть призвести і до утворення вакууму при спорожненні резервуара та викликати здавлювання його корпуса. Пропускна спроможність дихальних ліній та встановлених на них дихальних клапанів повинна відповідати швидкості закачування рідини в резервуар. При цьому необхідно враховувати виділення з рідини розчинених газів, особливо при закачуванні нестабільних нафт та бензинів.
Примерзання дихальних клапанів можна зменшити шляхом їх виготовлення з пластмас, фторопласту або футерівки пластмасою робочих поверхонь.
До утворення небезпечного тиску може також призвести несвоєчасне відкривання засувок на лінії, в яку подається продукт, неповне відкривання засувки або відключення лінії без попереднього попередження оператора насосної або компресорної станції.
Значна кількість аварій, що супроводжуються вибухами та пожежами, виникає при пуску компресорів із закритими засувками на викидних газових лініях.
Для запобігання аварій та пошкоджень з подібних причин необхідно:
- віддавати перевагу відцентровим насосам та компресорам;
- підбирати відцентрові насоси та компресори без значного перевищення їх характеристик над номінальними;
- у поршневих насосів та компресорів влаштовувати циркуляційну лінію з перепускним клапаном (рис.5.6);
- використовувати пристрої, які автоматично регулюють роботу насоса або компресора в залежності від величини тиску в лінії.

Рисунок 5.6 - Поршневий насос з циркуляційною лінією
1 - всмоктувальна лінія; 2 - нагнітальна лінія; 3 - поршневий насос; 4 - перепускний пристрій; 5 - циркуляційна лінія
Порушення теплового балансу апаратів. Багато хімічних процесів проходять з виділенням значної кількості тепла, з утворенням побічних продуктів у виді парів та газів. Надлишкове тепло, а також надлишкові газоподібні продукти своєчасно відводять з апарата, за рахунок чого в ньому підтримується нормальний робочий тиск.
З рівняння видно, що якщо збільшиться тепловиділення хімічної реакції при незмінному відведенні тепла з апарата або порушиться процес відводу надлишкового тепла, тоді за однієї і тієї ж кількості тепловиділень будуть збільшуватися всі останні складові правої частини рівняння теплового балансу. Збільшення приведе до зростання температури в апараті, підвищеного виходу побічних газів та пароподібних продуктів і зростання тиску в системі. Підвищення робочої температури в апараті, у свою чергу, викличе підвищення швидкості хімічної реакції, а отже, і збільшення тепловиділень в одиницю часу. Таким чином, створюються умови для лавиноподібного процесу зростання тепловиділень та різкого підвищення тиску, для переходу хімічної реакції у вибух.
Швидкість хімічної реакції може зростати не тільки в результаті підвищення температури, але і за відповідного порушення співвідношення речовин, що реагують, при збільшенні кількості каталізатора або ініціатора, що бере участь в реакції.
Зменшення кількості надлишкового тепла, що відводиться від апарата, відбувається через припинення подачі холодоагенту, забруднення теплообмінної поверхні холодильників твердими відкладеннями, зниження інтенсивності перемішування реагентів (зупинка мішалки) тощо. Подібні випадки спостерігаються при одержанні нітросполук, алюмінійорганічних сполук, пероксидів.
Підвищення тиску може виникати також за несвоєчасного відведення з реакторів надлишку газоподібних продуктів реакції, а також при утворенні пробок у відвідних та викидних лініях.
Для запобігання порушення теплового балансу апаратів (хімічних реакторів) необхідно:
- контролювати дозування хімічних речовин та каталізаторів автоматичними дозаторами;
- контролювати подачу необхідної кількості холодоагенту;
- своєчасно очищати теплообмінну поверхню від забруднень;
- забезпечувати своєчасне відведення газоподібних продуктів реакції, а за необхідності й автоматичне скидання надлишкового тиску. Викидні лінії виводять за межі приміщення або на факел, захищають від відкладень, своєчасно перевіряють надійність їх роботи.
Порушення температурного режиму роботи апаратів. Надзвичайно небезпечним випадком є утворення підвищеного тиску в апаратах і трубопроводах при нагріванні в них рідин і газів вище встановленої межі. Температурний режим може бути порушений через перегрів рідин та газів, що знаходяться у технологічному обладнанні. Перегрів також може виникнути через відсутність або несправність контрольно-вимірювальних приладів, недогляд обслуговуючого персоналу, вплив високонагрітих сусідніх апаратів, в результаті підвищеної температури навколишнього середовища. При цьому тиск в апаратах збільшується за рахунок об’ємного розширення речовин та збільшення пругкості їх парів та газів.
Необхідно розрізняти два види апаратів, в яких названі явища будуть проявлятися по-різному, - це апарати, що повністю ізольовані, та апарати, що поєднані з іншими.
Апарати з наявністю газів та перегрітої пари. Тиск у герметичних апаратах з газами або перегрітими парами збільшується прямо пропорційно зростанню їх температури:
(5.9)
деPп , - відповідно значення початкового та кінцевого тиску в апараті, Па;
, - відповідно початкова та кінцева температура речовини, К;
Z- коефіцієнт стиснення газу за відповідних значень тиску і температури (Z<1).
В апаратах, балонах та трубопроводах із стисненими газами небезпечний тиск можливий лише за значного підвищення температури. Відмічено немало випадків, коли під впливом високої температури пожежі розривались газові балони, перекриті дільниці газопроводів, газові лічильники, резервуари та апарати з парами і газами.
Апарати, що нормально заповнені горючими рідинами. В герметичних апаратах і ємностях, нормально заповнених рідинами, над рідинами є паровий простір визначеного об’єму. Тиск визначається пругкістю насиченої пари рідини за даної температури. З підвищенням температури, яка не перевищує температуру кипіння рідини, тиск в таких апаратах також підвищується.
Кінцевий тиск в апаратах з насиченими парами рідин і наявністю рідкої фази за зміни температури можна визначити з умови:
(5.10)
де - тиск насиченої пари за температури , Па.
При нормальному заповненні апарата рідиною газовий або паровий простір повинен бути достатнім, щоб виконувати роль компенсатора, тобто роль газового ковпака, і усувати небезпеку утворення надмірно великих тисків за підвищення температури. Але неповне заповнення апаратів та балонів в той же час зменшує їх корисну ємність, знижує коефіцієнт використання внутрішнього об’єму, робить дорожчою його експлуатацію.
Переповнені апарати та ємності. Особливу небезпеку представляють герметичні ємності та трубопроводи, що повністю заповнені рідиною або скрапленим газом. При заповненні таких апаратів, ємностей, балонів дуже часто виникають випадки їх переповнення. При цьому рідина займає весь об’єм апарата, і вільного парового простору в ньому немає. Оскільки рідини практично не стискаються, нагрівання їх навіть до невисоких температур викликає дуже великі внутрішні тиски, які приводять до пошкоджень та розриву стінок апаратів. На практиці є немало випадків, коли невірне заповнення бочок та цистерн рідинами, а ємностей і балонів скрапленими газами з наступним нагріванням закінчувалося аваріями. Характерними у цьому відношенні є аварії, які пов’язані з розривами стінок сферичних резервуарів з рідким газом на нафтопереробних підприємствах (через добові зміни температури навколишнього середовища).
Приклад аварії. На одному з нафтопереробних заводів виникло руйнування сферичного резервуара об’ємом 600 м3, що був заповнений бутан-бутиленовою фракцією за температури повітря нижче 00С. Всі лінії були відключені, а на місці влаштування запобіжного клапана була встановлена заглушка. До ранку температура навколишнього середовища підвищилася, що викликало сильне підвищення тиску рідини та розрив стінок резервуара. Рідкий газ, що виливався назовні, швидко випаровувався, утворюючи при цьому газову хмару, яка рухалася за вітром у бік виробничих установок. Спалахування газу виникло від факелів полум’я форсунок трубчастих печей. В результаті цього вогнем були охоплені технологічні установки та резервуари з нафтопродуктами.
Підвищення температури на величину ∆Т викликає збільшення об’єму рідини, яка знаходиться в ємності, і деяку зміну об’єму самої ємності, причому об’єм рідини змінюється значно більшою мірою, ніж об’єм ємності. Стінки ємності гасять намагання рідини до розширення, ніби стискають її, за рахунок чого в ємності виникає надлишковий тиск ∆Р.
Приріст тиску в переповнених апаратах або трубопроводах (при їх нагріванні без врахування зміни розмірів апаратів) визначають за формулою:
(5.11)
де ΔP - приріст тиску, Па;
β - коефіцієнт об'ємного розширення рідини, 1/град;
- коефіцієнт об'ємного стиснення рідини, ;
- зміна температури в апараті, .
Коефіцієнти об’ємного розширення, стиснення та лінійного розширення змінюються за зміною температури, тому при розв’язанні задач необхідно брати їх середнє значення (у заданому інтервалі зміни температур).
Загальний тиск в апараті, що нагрівається, можна визначити з наступного співвідношення:
(5.12 )
де – загальний тиск в апараті, Па;
– робочий (початковий) тиск рідини за даної температури, Па;
- приріст тиску в апараті за рахунок підвищення температури, Па.
Дотримання температурного режиму роботи апаратів досягається за допомогою проведення наступних профілактичних заходів:
- обладнання апаратів контрольно-вимірювальними приладами або автоматично діючими регуляторами температури;
- захист апаратів та ємностей від випромінювання зовнішніх джерел тепла теплоізоляцією, екрануванням, пофарбуванням поверхні в білий колір. Величина захисного шару теплоізоляції апаратів та трубопроводів, а також товщина земляної засипки підземних резервуарів повинні бути такими, щоб температура усередині апарата за період впливу зовнішнього джерела тепла не могла піднятися понад встановлену величину;
- розміщення обладнання з горючими речовинами на визначених відстанях від приладів опалення та інших джерел тепла (наприклад, балони та інші переносні ємності з горючими газами і рідинами забороняється розташовувати ближче, ніж за 1-2 м від джерел тепла);
- захист апаратів запобіжними клапанами;
- контроль за ступенем заповнення апаратів горючими рідинами та скрапленими газами за допомогою пристроїв, що сигналізують про межу їх заповнення. При обладнанні ємностей із скрапленими газами таким пристроєм подача першого сигналу повинна проводитися при заповненні резервуара не більше ніж на 80%. При заповненні газових балонів кількість скрапленого газу, що подається, контролюється за масою.
Для створення оптимальних умов безпеки та економічності необхідно визначати максимально можливий ступінь заповнення ємностей рідиною або скрапленим газом.
В приблизних технічних розрахунках величина вільного простору в ємності, апараті та трубопроводі визначається наступним чином:
(5.13)
де – об’єм вільного від рідини простору в апараті, м3;
∆ – максимальний перепад температур при експлуатації даного апарата, 0С;
β – коефіцієнт об’ємного розширення рідини, 1/град.
Таким чином, ступінь заповнення резервуарів та ємностей ε повинен бути не більшим за наступну величину:
(5.14)
На практиці для забезпечення безпеки ступінь заповнення повинен бути:
- для ємностей та судин з скрапленими газами ε ≤ 0,85-0,9;
- для ємностей та судин з горючими рідинами ε ≤ 0,9-0,95.
Встановлену норму заповнення апаратів перевищувати не можна для запобігання їх розриву при можливому перегріві. Забороняється також наглухо відключати окремі ділянки трубопроводів, заповнені скрапленими газами та іншими горючими рідинами, якщо в них можлива зміна температури. В цьому випадку на технологічній лінії закривають лише одну засувку.
Порушення процесу конденсації парів. В основі багатьох технологічних процесів виробництв - процеси випаровування горючих та легкозаймистих рідин. До таких процесів відносяться: перегонка та ректифікація розчинів на атмосферних та вакуумних установках, випаровування розчинників із розчинів, твердих речовин тощо. У кожному випадку випаровування рідини пов’язане з наступною конденсацією одержаної пари (рис.5.7). Однією з найбільш поширених причин підвищення температури, а отже, і тиску в ректифікаційній колоні та в інших апаратах, що пов’язані з нею, є порушення нормального процесу конденсації пари. У цьому випадку конденсація зменшується або зовсім припиняється в результаті зменшення кількості тепла, що відводиться від апарата з парою за незмінної кількості тепла, яка поступає до апарата від підігрівника. Тобто конденсація пари зменшиться або зовсім припиниться, а процес пароутворення буде продовжуватися, що призведе до накопичення кількості пари в колоні, конденсаторі та інших апаратах з наступним підвищенням тиску. При цьому частина пари, яка не сконденсувалася, буде виходити назовні через дихальну лінію на ємності конденсату, утворюючи навколо неї горючу суміш з повітрям.
Приріст тиску в системі в результаті порушення процесу конденсації пари можна визначити за формулою:
(5.15)
де - коефіцієнт неповноти конденсації пари, %;
- продуктивність апарата за парою, кг/с;
τ- тривалість порушення нормального режиму конденсації, с;
- густина пари рідини за робочих температури та тиску в апараті, кг/м3;
- вільний об’єм системи, м3;
- тиск навколишнього середовища, Па
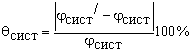
Рисунок. 5.7 - Установка ректифікації розчинів
1- колона; 2-конденсатор-холодильник; 3-прийомник конденсату; 4- повітряна труба ємності; 5- підігрівник
Причиною порушення нормального процесу конденсації є зменшення або повне припинення подачі холодоагенту (води, розсолу, скрапленого газу тощо) або надходження його з більш високою початковою температурою, а також зменшення коефіцієнта теплопередачі від пари до холодоагенту за рахунок сильного забруднення теплообмінної поверхні відкладеннями з малою теплопровідністю.
Коефіцієнт неповноти конденсації в загальному виді можна представити наступним відношенням:
(5.16)
де – кількість тепла, що передається через теплообмінну поверхню при повній конденсації пари, ккал/год;
– кількість тепла, що передається при порушенні процесу конденсації пари, ккал/год.
В деяких випадках процеси ректифікації та випаровування розчинів проходять під вакуумом за більш низьких температур. Це необхідно не тільки з технологічних розумінь, але і в деяких випадках у зв’язку з необхідністю зниження пожежовибухонебезпеки процесу. Зниження температурного режиму зменшує можливість протікання в апаратах небажаних процесів термічного розкладання, полімеризації, коксоутворення тощо. Вакуум в системі створюється за рахунок конденсації парової фази та примусового відсмоктування з конденсатора спеціальним вакуум-насосом або вакуум-ежектором парів і газів, які не сконденсувалися. Якщо знизиться продуктивність або повністю зупиниться робота вакуум-насоса (ежектора), тоді вакуум порушиться і в системі виникне підвищений тиск. Величину приросту тиску в цьому випадку можна також визначити за формулою (5.15), а коефіцієнт неповноти конденсації парів - умовно визначити з наступного відношення:
(5.17)
де – нормальна продуктивність вакуум-насоса або ежектора, м3/год;
– дійсна продуктивність вакуум-насоса або ежектора, м3/год.
Зниження пожежної небезпеки від порушення нормального процесу конденсації парової фази досягається впровадженням наступних заходів протипожежного захисту:
- забезпечення безперервного контролю за величиною тиску в ректифікаційних колонах та випарних апаратах. Доцільно обладнувати апарати приладами автоматичного регулювання подачі охолоджуючої рідини (холодоагенту) в конденсатори, у залежності від тиску та температури парів, що поступають на конденсацію;
- контроль температури холодоагенту перед його надходженням до конденсаторів та після виходу з них. Не допускається підвищення понад встановленої величини температури холодоагенту після виходу його з конденсатора. Застосовують автоматичну систему регулювання кількості холодоагенту, що подається в конденсатори, в залежності від величини температури при виході його з конденсатора;
- регулярно проводити очистку теплообмінної поверхні від відкладень;
- контролювати роботу вакуум-насосів або вакуум-ежекторів, не допускати зниження їх продуктивності;
- при припиненні подачі холодоагенту або зупинці роботи вакуум-системи необхідно швидко (автоматично) припинити роботу апарата, який відповідає за вироблення пари. З цією метою застосовують конденсатори заглибного типу, а не кожухотрубчасті. Велика кількість холодоагенту в чаші заглибного конденсатора забезпечує конденсацію пари протягом 15-20 хвилин після припинення подачі холодної води або розсолу в конденсатор. За цей час можна ліквідувати неполадки або зупинити процес. Основний недолік таких конденсаторів – займають великі виробничі площі.
Потрапляння рідин з низькою температурою кипіння до високонагрітих апаратів. Якщо в апарат з високою робочою температурою потрапляє рідина, температура кипіння якої значно нижча за температуру в апараті, тоді відбудеться інтенсивне випаровування рідини і підвищення тиску.
Приклад аварії. На одному з нафтопереробних підприємств при пуску вакуумної колони в неї при температурі 3700С в результаті помилкового переключення ліній відкрили доступ бензину. Перші порції бензину, що потрапили до колони, випарувалися, підвищився тиск, який призвів до розриву корпусу апарата, - виникла пожежа.
Рідини, що мають низьку температуру кипіння (вода, бензин тощо), попадають до високотемпературного апарата разом з продуктами, що надходять до нього, через нещільності теплообмінної поверхні холодильників (що знаходяться усередині апаратів), при невірному переключенні ліній, у виді конденсату з парових технологічних та продувних ліній. При контакті рідини з низькою температурою кипіння з високотемпературним продуктом (або з корпусом апарата) виникає інтенсивне випаровування рідини з низькою температурою кипіння і тиск значно підвищується.
Приріст тиску у високотемпературних апаратах при попаданні в них рідин з низькою температурою кипіння та швидкому їх випаровуванні визначають за формулою:
(5.18)
де - тиск навколишнього середовища, Па;
m - маса рідини з низькою температурою кипіння, яка потрапила до апарата і випарувалася в ньому, кг;
- вільний об’єм системи, м3;
Тр- робоча температура в апараті, К;
M- молекулярна маса рідини, що потрапила до апарата, кг/кмоль.
Слід відмітити, що при розв’язанні практичних задач, необхідно враховувати те, що рідина, яка потрапила в нагрітий апарат, може випаруватися не повністю. Кількість рідини, що при цьому випарувалася, буде залежати від багатьох умов, в тому числі й від числа робочих параметрів апарата, кількості та властивостей речовини, нагрітої до високої температури, кількості рідини, що потрапила до апарата, її властивостей та початкової температури. Для приблизного вирішення цього питання достатньо скласти рівняння теплового балансу.
Для запобігання попаданню рідин з низькою температурою кипіння до апаратів, нагрітих до високих температур, необхідно:
- на лініях подачі гострої водяної пари (з метою обігріву, перемішування, продувки, видавлювання речовин) влаштовувати пристрої для спуску конденсату (рис. 5.8);
- для запобігання конденсації пари подавати її тільки в достатньо нагріті (понад 1000С) апарати;
- контролювати наявність в апаратах залишків рідин, що можуть бути наявні після промивки їх або гідравлічного випробування;
- контролювати кількість води в сировині, яка підлягає нагріву.
|