|
Запобіганню утворенню горючого середовища в закритих апаратах, ємностях та трубопроводах з газами сприяють наступні інженерно-технічні рішення:
1. Підтримання концентрації горючого газу у суміші з окислювачем за концентраційними межами поширення полум’я (якщо це можливо за умовами технології). За наявності суміші горючого газу з окислювачем робоча концентрація в апаратах повинна бути вище верхньої або нижче нижньої концентраційної межі поширення полум’я з урахуванням коефіцієнтів безпеки:
(2.14)
Для цього на лініях подачі встановлюють автоматичні регулятори співвідношення, витрати та тиску газів. Особливо це стосується вибухонебезпечних газофазних окислювально-відновлювальних процесів, безпека яких обумовлюється не тільки співвідношенням горючих компонентів, що змішуються з окислювачами, але і відношенням регламентованої швидкості подачі реагентів. Так, наприклад, в процесі окислення аміаку виробництва азотної кислоти підтримується робоча аміачно-повітряна суміш, що вміщує 9,5- 11% NH3 та 90,5-89% повітря при концентраційних межах поширення полум’я аміаку 15-28%, а також регулюється швидкість подачі аміаку (в м3/год) при стабільному потоку повітря або повітря за постійної витрати аміаку.
2. Підтримання в газових комунікаціях надлишкового тиску, що сприяє запобіганню підсмоктування зовнішнього повітря через нещільності. Прикладом цього можуть бути трубопроводи факельних систем, по яких безперервно або періодично скидаються горючі гази на спалювання або утилізацію.
3. Безперервний автоматичний контроль вмісту небезпечної домішки в газі (окислювача в інертному газі, окислювача в суміші горючого та інертного газу, горючого газу в окислювачі). Наприклад, контроль домішки повітря або кисню в азото-водневій суміші перед стисканням на компресорах в агрегатах синтезу аміаку. Для контролю домішок апарати і трубопроводи обладнують газоаналізаторами, а також передбачають блокування на вузлах засувок, що виключає потрапляння домішок у технологічний газовий потік. Якщо в потоках сировини знаходиться незначна кількість домішок, які в даному процесі можуть перетворюватися в інші сполуки або переходити в інший агрегатний стан та накопичуватися в технологічному обладнанні, утворюючи вибухонебезпечні суміші, то установлюють максимально припустиму кількість їх в працюючій апаратурі. Кількість таких домішок в кожному конкретному випадку повинна бути обґрунтована і не представляти небезпеки утворення вибухонебезпечних сумішей.
4. Стабілізація зони горіння горючої суміші в захищеному просторі апарата (реактора) шляхом вибору швидкості та режиму руху горючої суміші, що запобігає "проскакуванню полум'я" (переміщення зони горіння) у незахищений простір апарата (реактора).
5. Зміна стану горючої суміші при аварійних ситуаціях за допомогою інертного розріджувача або шляхом припинення подачі одного із компонентів горючої суміші, у деяких випадках - припинення подачі відразу двох компонентів. Це забезпечує швидке переведення горючої суміші в негорючий стан. Слід зазначити, що за технологічними або економічними міркуваннями деякі процеси приходиться здійснювати при концентрації окислювача в газовому середовищі в межах спалахування суміші з горючими газами.
Таким прикладом може служити агрегат конверсії метану в газовому цеху виробництва аміаку (рис. 2.12).
На початкових стадіях експлуатації таких агрегатів більша частина сталевих компенсаторів виходить з ладу в результаті прогару. Горіння відбувається при температурі близько 1700°С, тому в момент досягання полум’ям компенсаторів, що не захищені вогнетривкою футеровкою, сталь плавиться і газ у виді полум’я виривається в цех і створює там обстановку пожежі. В цьому випадку для припинення горіння необхідно перекрити подачу газу в конвертор. Застосовується автоматичне перекриття шляхом подачі сигналів з термопар, що встановлені над каталізатором та в трубопроводі біля компенсатора. Крім цього, передбачена подача азоту в камеру змішування.
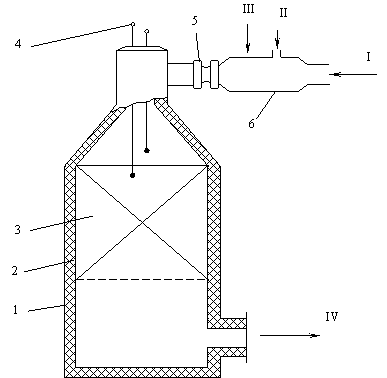
Рисунок 2.12 - Конвертор метану
1 – корпус; 2 – футировка; 3 – каталізатор; 4 – термопара; 5 – компенсатор; 6 – змішувач; I – киснево-повітряна суміш; II – метан; III – азот; IV – газ конверсії
Таким чином, вибухобезпека газової суміші забезпечується флегматизацією інертним газом, що подається постійно в технологічну систему з безперервним автоматичним контролем складу трикомпонентної газової суміші (горючий газ, окислювач, інертний газ). В таких процесах потрібно здійснювати постійний автоматичний контроль подачі інертного розріджувача в кількостях, необхідних для забезпечення мінімальної концентрації окислювача, що поступає до газового змішувача. Необхідний також постійний нагляд за станом газоаналізаторів та засобів регулювання подачі інертного середовища.
|