секції, що включає в себе завантажувальну секцію 1 із широким завантажувальним вікном 2, сполученим із зйомною завантажувальною лійкою 3, секції 4, 5, 6 із непроникною стінкою і зеєрні секції 7, 8. Ці секції розташовані в наступній послідовності: завантажувальна секція 1, секції 4, 5 із непроникною стінкою, зеєрна секція 7, секція 6 із непроникною стінкою, зеєрна секція 8.
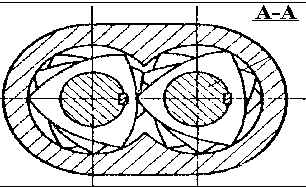
Рис. 3.2 - Поперечний перетин насадок - трикутників Релло
На виході робоча камера оснащена матрицею 9, призначеною для виводу з робочої камери готового сухого порошку. Секції робочої камери уніфіковані за формою, поперечними розмірами і довжиною. При цьому вони виконані порожнистими і сполучені одна з іншою торцями, так що разом їхні порожнини утворюють порожнину 10 робочої камери. Довжини зеєрних секцій 7, 8 однакова. Довжина секцій 4, 5, 6 із непроникною стінкою дорівнює довжині завантажувальної секції 1. При цьому вона в 1,17 рази перевищує довжину секцій 7, 8. Стінка зеєрних секцій 7, 8 утворена з зеєрних колосників (на кресленні не показані), розташованих на певному віддалення один від одного. Кожна секція 4, 5, 6 із непроникною стінкою оснащена резисторним електронагрівальним елементом 11, розташованим навколо її стінки з зовнішнього боку. Всі електронагрівальні елементи 11 підключені до зовнішнього регульованого джерела електроенергії (на кресленні не показане). До керуючого входу цього джерела електроенергії підключено термодатчик 12, виконаний, наприклад, у вигляді термопари. Термодатчик 12 установлений на кінцевій ділянці стінки зеєрної секції 7 поблизу торця секції 6 із непроникною стінкою.
У порожнині 10 робочої камери розміщені два прямих збірних шнекові вали з однаковим напрямком обертання. Ці вали розташовані паралельно і сполучені один з одним. Кожний шнековий вал містить у собі привідний вал 13, а також жорстко закріплені на ньому десять шнеків 14...23 і чотири групи 24...27 роздрібнюючих насадок. Ці шнеки і групи насадок встановлені в наступній послідовності: шнеки 14, 15; група 24 роздрібнюючих насадок; шнеки 16, 17; група 25 роздрібнюючих насадок; шнеки 18, 19; група 26 роздрібнюючих насадок; шнек 20; група 27 роздрібнюючих насадок; шнеки 21, 22, 23. Привідний вал 13 кінематично пов'язаний через роздвоювач із редукторним елементоприводом (на кресленні не показані). Шнеки 14. . . 23 мають однаковий напрямок витків, однаковий діаметр і постійний крок витків. Для того, щоб на всьому шляху просування порошку, що переробляється, уздовж порожнини 10 робочої камери аж до матриці 9 напірне зусилля, що діє на цей матеріал, було постійним за величиною, кожний наступний шнек 15. . . 23, крім шнеків 16, 17, виконаний із меншим кроком витків, ніж попередній.
Насадки, що здрібнюють, складають групи 24...27 насадок і виконані в такій формі, що в перетині, перпендикулярному до осі симетрії валів, вони мають вигляд рівностороннього трикутника з круглим вирізом у центральній частині, що має дугоподібні сторони (трикутники Релло). Кожні дві насадки, що роздрібнюють, мають форму трикутників Релло і розташовані в одній площині, установлені із забезпеченням постійного контакту. Насадки кожного шнекового вала, що роздрібнюють, зміщені одна відносно одної на кут, рівний 5° , з утворенням гвинтового каналу, напрямок якого в групах 24, 25, 26 роздрібнюючих насадок, збігається з напрямком витків шнеків 14...23, а в групі 27 роздрібнюючих насадок, протилежний напрямку витків цих шнеків. Групи 24, 25 складаються з п'ятьох роздрібнюючих насадок, кожна і розташовані відповідно в секції 4 і секції 5 із непроникною стінкою. Групи 26, 27 роздрібнюючих насадок, складаються відповідно з чотирьох і трьох насадок, що роздрібнюють, і розташовані усередині секції 6 із непроникною стінкою.
Тепловий режим усередині зеєрної секції 7 підтримується на оптимальному рівні за допомогою термодатчика 12, що реєструє температуру стінки. За сигналами цього термодатчика регулюється кількість енергії, яка підводиться до електронагрівальних елементів 11 від зовнішнього регульованого джерела електроенергії. Після обробки екструдером, наприклад, порошку ПС-1 забезпечується такий його склад, що має і ефективні інгібіруючі властивості. Його щільність 0,7—0,9 кг/л, він складається з Na2С3 (більше 90%) і добавок, що перешкоджають злежуванню (2% стеаратів металів, 0,5% стеаринової кислоти і 1% графіту). При цьому вологість порошку не перевищує 0,5% , а середній розмір часток порошку становить 0,11— 0,45 мм. Це значно більше, ніж для порошків аналогічного складу, що застосовуються за рубежем, що знижує його вогнегасну здатність.
Однак склад ПС-1 розробляється для гасіння металів і такий ступінь дисперсності є найбільш зручним для цієї мети. Виготовлений вогнегасний склад ПСБ являє собою дрібний сипучий порошок білого кольору із сірим чи рожевим відтінком (розмір часток 0,12—0,01 мм). Насипна щільність - 0,9 -1,2 г/см3 (неущільненого). Вологість порошку не перевищує 0,5%.
До позитивних якостей розглянутого екструдера слід віднести його високу продуктивність та спроможність досягати однаковості у розмірах часток вогнегасного порошку. Такий помол досягається завдяки використанню кулачків для здрібнювання у вигляді трикутників Релло (рис.3.3). Тому далі розглянемо більш детально схему синхронного обертання двох кулачків, які забезпечують постійний точковий дотик.